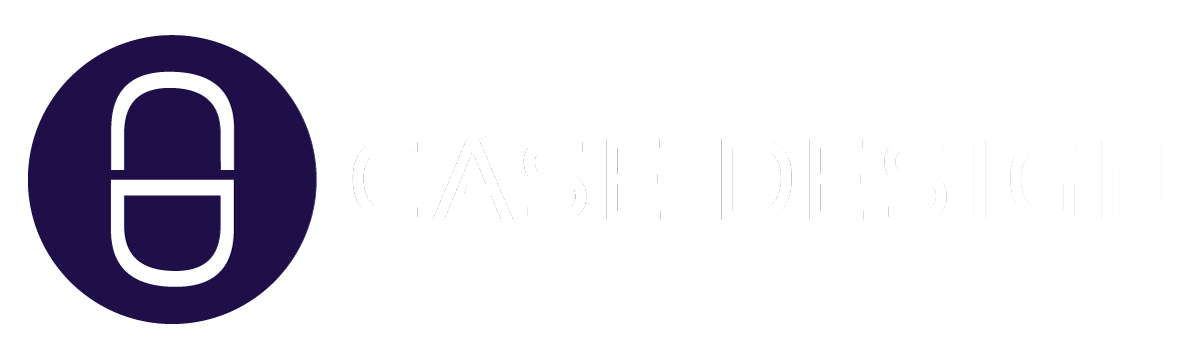
Case Design use Carveco for custom foam cutting & flight case manufacture
Case Design is a UK manufacturer of custom flight cases and foam inserts used to protect high value equipment and accessories, such as cameras and lenses for the broadcast and filming industry. Their custom foam inserts and cases have also been used to protect medical and electrical components, defence equipment and even a boomerang. Just about anything you can think of!
As specialists in their field, Case Design moved away from hand-carving foam over 9 years ago, in order to provide faster, more accurate solutions for their international customer base. Mark Harley, Director at Case Design comments, “We used to cut everything by hand on our bandsaws using templates of the equipment and our team of highly skilled operatives. We changed our modus operandi when we purchased a CNC router as part of our modernization program.”
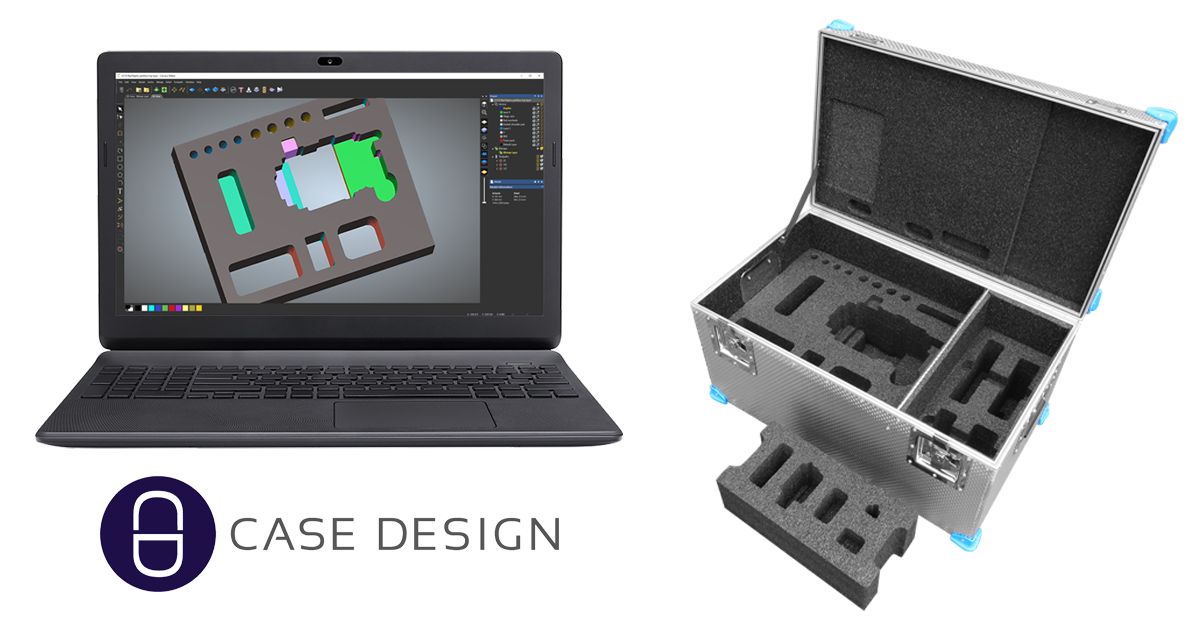
Now they can start a custom design by taking detailed measurements and drawings of the piece before importing it into their CAD (Computer-Aided Design) Software, AutoCAD. They then create the required vector drawings which are sent to the customer for review. Once approved, the full design is imported into Carveco to create the necessary toolpaths to cut the inserts on their AXYZ 5010 CNC router. Thanks to Carveco’s ability to preserve the layers created in AutoCAD, this takes less than 5 minutes for an average design and no more than 10 minutes for complex drawings with more than 20 layers.
To do this, Case Design simply select the vector shape for the recess/ pocket, choose the depth it needs to be CNC machined and the required cutting tools using Carveco’s Area Clearance toolpath strategy.
“One of the key features of Carveco over rival software is the ability to use multiple tools for the same bit of CNC cutting within a vector shape. To give an example, say we need a 200mm square with a 4mm radius corner to be cut 100mm deep. As big tools cut foam far more cleanly, we would use the ‘workhorse’ 19mm cutter to remove 99% of the material in about 2 mins. We would then use a 8mm tool to remove the last bit of material from the corners.
Rival software would make us run the entire program again with the 8mm tool, which would have to cut fresh air for 99% of the time until it reached the corners – this would probably take about 30 minutes!”
To prevent any unnecessary wastage of their foam blocks, Case Design always run Toolpath Simulations prior to machining. These allow Case Design to not only visualise what the custom foam insert would look like complete, but also at each stage of cutting. This helps to identify any problematic areas. Mark particularly “loves the option to see the toolpaths in different colours”, using Carveco’s Enhanced Colour Simulation option. This allows users to apply a specific colour to each toolpath, which when simulated helps to quickly identify where the CNC tool is or is not cutting the foam.
“We would definitely recommend Carveco. It is excellent software. Not only is it easy to use but it is also very powerful in its ability and reasonably priced too.”
In addition, if requested by the customer, Case Design are able to send a render of the foam insert design in a variety of file formats such as PNG, JPEG and 3D PDF amongst others to the customers for final sign-off by using the Export View feature.
To house the equipment, Case Design also use Carveco to cut out the panels for their custom wooden flight cases. Using the Nesting functionality within Carveco, they can optimally position the vector shape for each case panel on the material to be cut to reduce wasting any material. These are then cut out using the profiling toolpath.